Reynolds Technology
Walking into the factory the smell of oil and grease being heated mix with the sounds of pistons pushing metal rods to shape tubes, grinders and polishers whirl in the background while the Reynolds workforce move from station to station to carry out the various activities it takes to produce their vast range of bicycle tubes.
Reynolds Technology, founded in 1898 in Birmingham, England, is one of the most renowned manufacturers of high-performance steel tubing for bicycles. Originally an offshoot of the Reynolds Tube Company, the brand became famous for its pioneering work in butted tubing, which reduced weight while maintaining strength—an essential advancement for competitive cycling.
In 1935, Reynolds introduced its groundbreaking 531 tubing, an alloy of manganese, molybdenum, and carbon steel. This became the gold standard for racing and touring bicycles for decades, used by legendary riders such as Eddy Merckx and Miguel Induráin. In 1976, Reynolds revolutionized the industry again with its 753 tubing, the first heat-treated steel tubing for bicycles, offering an unparalleled strength-to-weight ratio.
As materials evolved, Reynolds continued to innovate, introducing 853 in the 1990s—an air-hardening steel that became a favorite among frame builders. Today, Reynolds produces a wide range of tubing, including stainless steel options like 931 and 953, catering to modern steel bike enthusiasts.
Despite competition from aluminum, titanium, and carbon fiber, Reynolds steel remains a favorite among custom frame builders, offering a perfect blend of durability, ride quality, and craftsmanship. The brand's legacy endures as a symbol of British engineering excellence in the cycling world.
The Process
The process of making Reynolds bicycle tubing begins with high-quality steel alloys, such as manganese-molybdenum or stainless steel, which are carefully selected for their strength and performance properties. The raw material is heated and rolled into seamless cylindrical tubes, ensuring uniformity and eliminating weak points associated with welded tubing.
One of Reynolds’ key innovations is butting, a process where tubes are drawn through precision dies to create varying wall thicknesses—thicker at the ends for strength and thinner in the middle to reduce weight. Depending on the tubing series, single, double, or triple butting is applied to optimize strength-to-weight ratios.
For premium tubing like 853 and 953, an air-hardening process is used, where the material gains strength after welding due to molecular changes in the steel. Some alloys also undergo heat treatment to further refine their mechanical properties. Once formed, tubes are precision-cut, shaped, and checked for consistency.
Finally, each tube is carefully inspected, ultrasonically tested, and marked with the Reynolds decal—a hallmark of quality and craftsmanship. This meticulous process ensures that Reynolds tubing maintains its reputation as a top choice for frame builders worldwide, offering the perfect balance of strength, weight, and ride quality.
Reynolds Tubing in the Modern Age: Innovation, Sustainability, and Ride Quality
Reynolds Technology has remained a cornerstone of the cycling industry, continuously refining its steel tubing to meet the evolving demands of modern riders. While aluminum and carbon fiber dominate mainstream bike manufacturing, steel remains a preferred material among custom frame builders and cyclists who prioritize ride quality, longevity, and sustainability.
Eco-Friendly Benefits of Reynolds Tubing
In an era of growing environmental consciousness, steel is making a resurgence as a sustainable alternative to carbon fiber. Carbon frames, though lightweight and widely used in high-performance cycling, present a significant environmental challenge due to their energy-intensive manufacturing and difficulty in recycling. Once a carbon frame reaches the end of its lifespan, it often ends up in a landfill.
Steel, on the other hand, is fully recyclable and can be repurposed indefinitely without degrading its material properties. Reynolds tubing is manufactured with this in mind, offering a sustainable choice for cyclists who seek durability and responsible production. Moreover, steel bikes have a much longer service life than carbon or aluminum, reducing waste and the need for frequent replacements. The repairability of steel also means that a damaged Reynolds frame can often be restored rather than discarded, further enhancing its environmental credentials.
Reynolds’ stainless steel 921 and 953 tubing offer corrosion resistance, ensuring longevity even in harsh riding conditions. This extends a bicycle's usable lifespan, reducing the environmental footprint associated with frequent frame replacements. Additionally, Reynolds is committed to responsible material sourcing and efficient production techniques, minimizing waste and energy use.
How Different Reynolds Tubes Affect Handling and Ride Quality
The characteristics of a bicycle frame—stiffness, compliance, and responsiveness—are largely determined by the tubing selection. Reynolds offers a range of tube sets, each tailored to different riding styles and performance needs.
Reynolds 531: The legendary tubing that defined steel bicycles for decades, known for its smooth ride quality and excellent fatigue resistance. Though heavier than modern alloys, it remains a favorite for touring and classic steel builds.
Reynolds 725: A heat-treated version of 525, offering increased strength and allowing for thinner-walled tubing. This results in a livelier ride and reduced weight without sacrificing durability.
Reynolds 853: A breakthrough air-hardening steel that gains strength after welding. This allows frame builders to use even thinner tubing, reducing weight while maintaining strength. The result is a lively, responsive ride with excellent power transfer—ideal for high-performance road and gravel bikes.
Reynolds 953: A premium stainless steel tubing with a strength-to-weight ratio comparable to titanium. It offers a combination of stiffness and compliance, making it a top choice for riders who want a balance of efficiency and comfort.
Tube diameter and wall thickness also play a crucial role in handling. Larger-diameter tubing increases frame stiffness, improving power transfer and sprinting performance but potentially reducing comfort. Thinner-walled tubing enhances compliance, absorbing road vibrations and making for a smoother ride over long distances. This balance is why Reynolds tubing remains a go-to choice for endurance and touring bikes, where comfort over extended periods is essential.
Ultimately, Reynolds continues to be at the cutting edge of steel bicycle technology, providing riders with materials that combine tradition, innovation, and sustainability. Whether for classic steel road bikes, rugged adventure builds, or high-performance racing machines, Reynolds tubing offers unmatched versatility and longevity in the modern cycling industry.
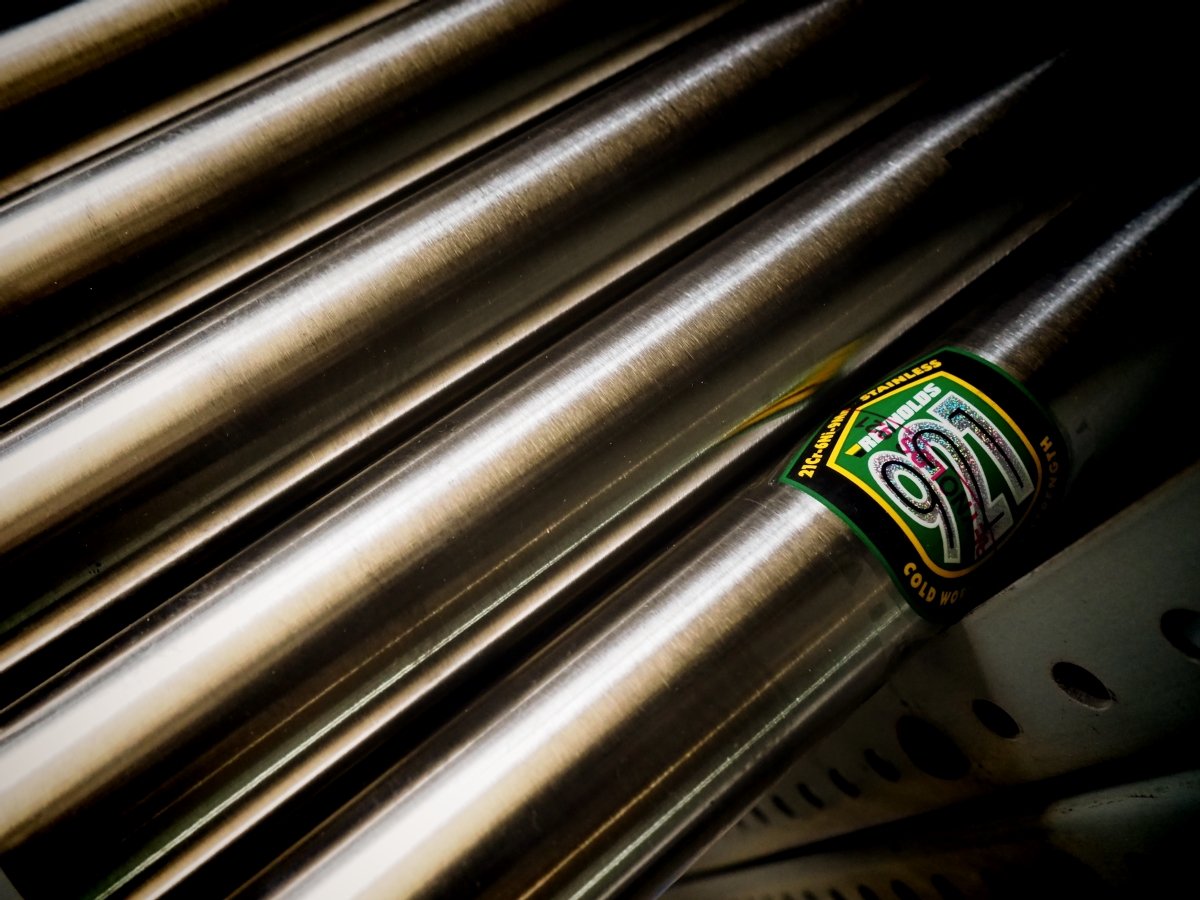
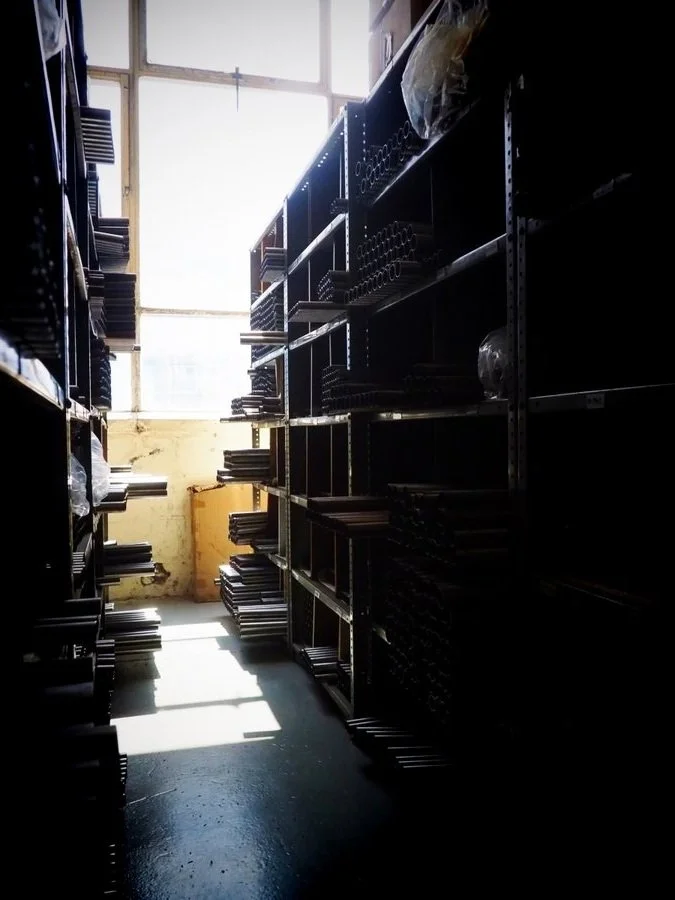
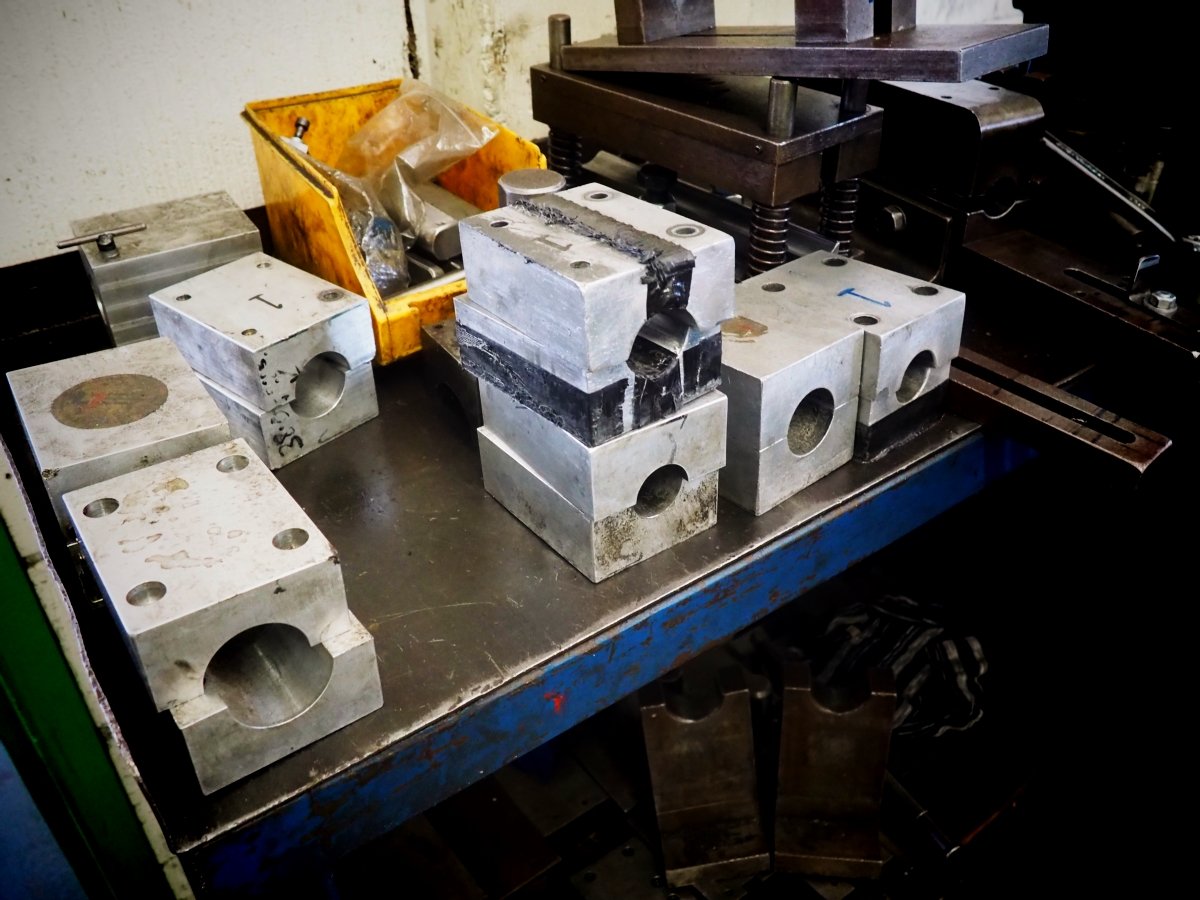
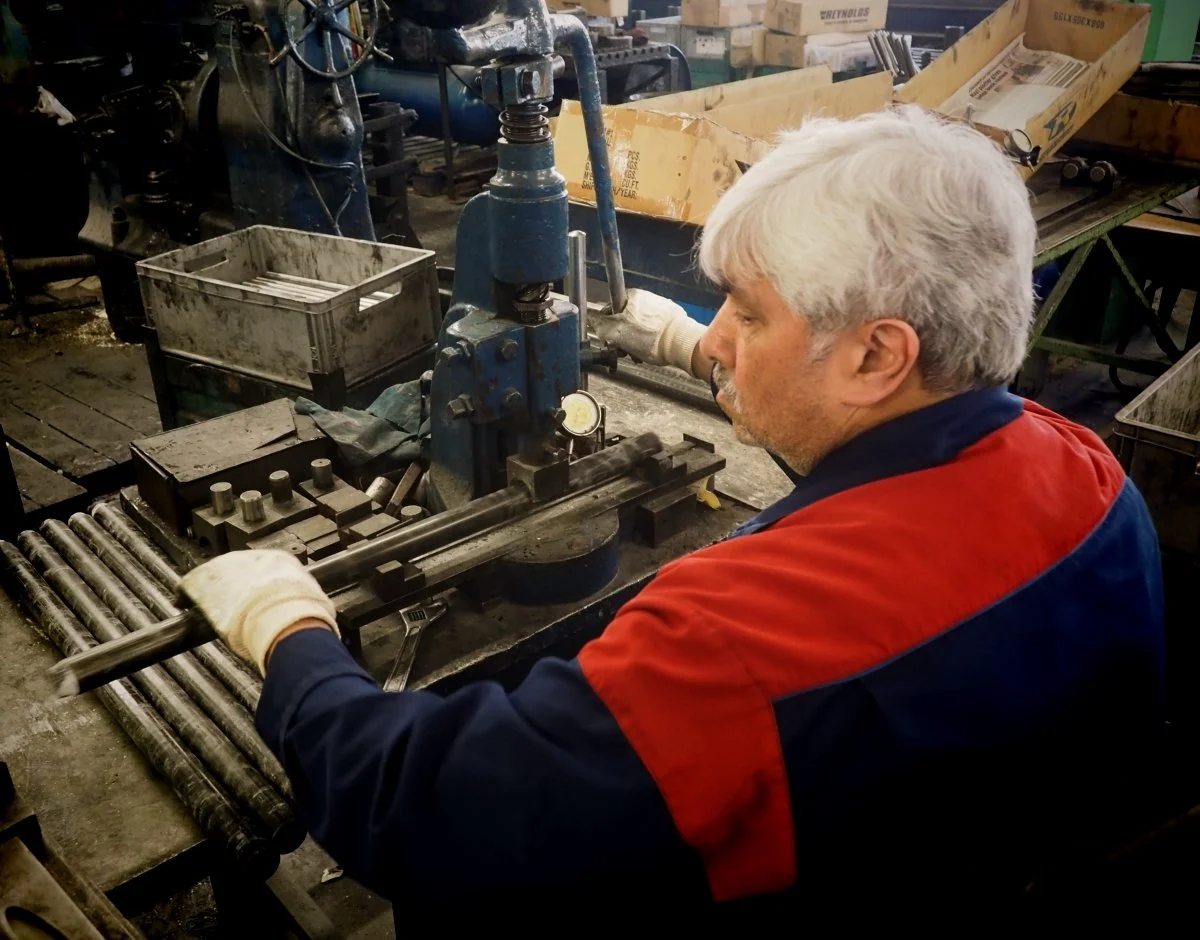
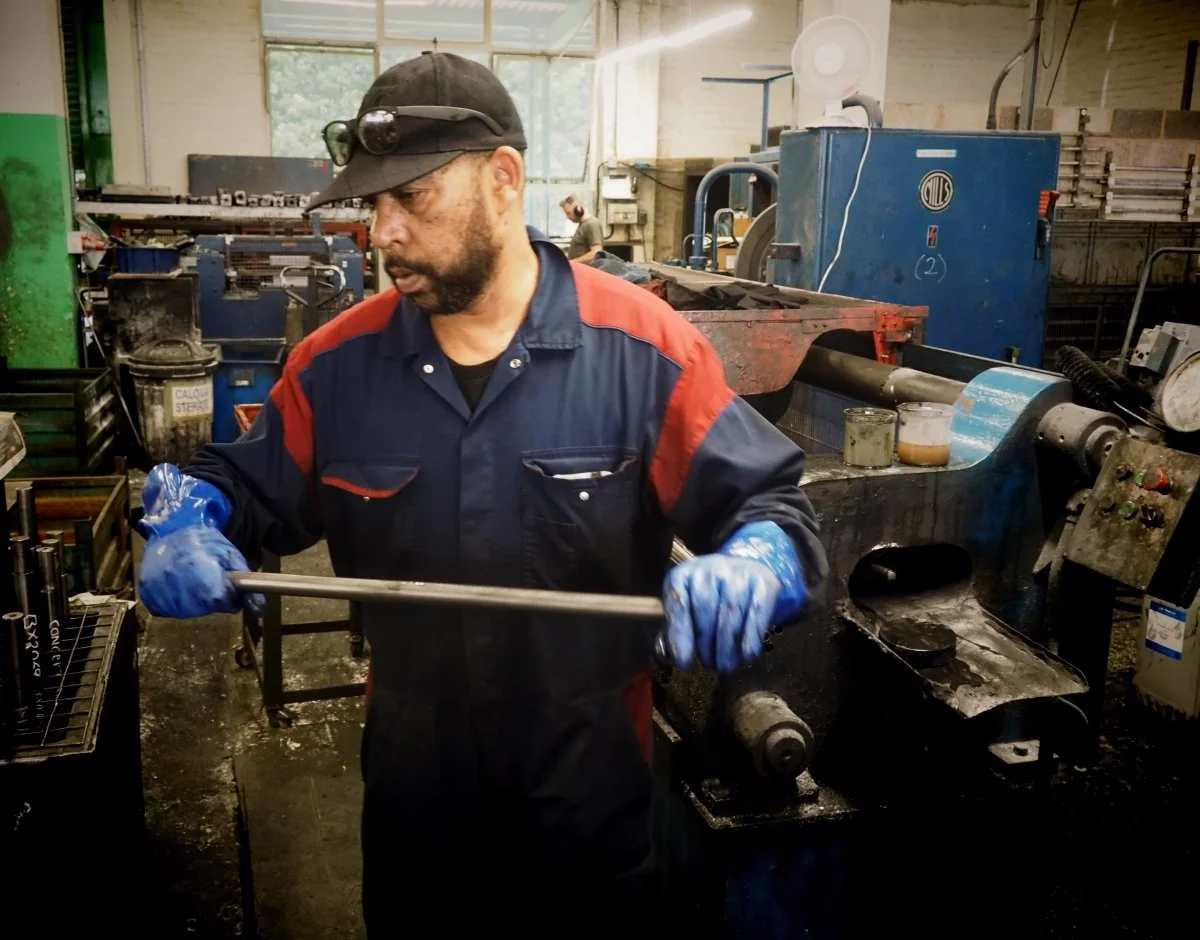
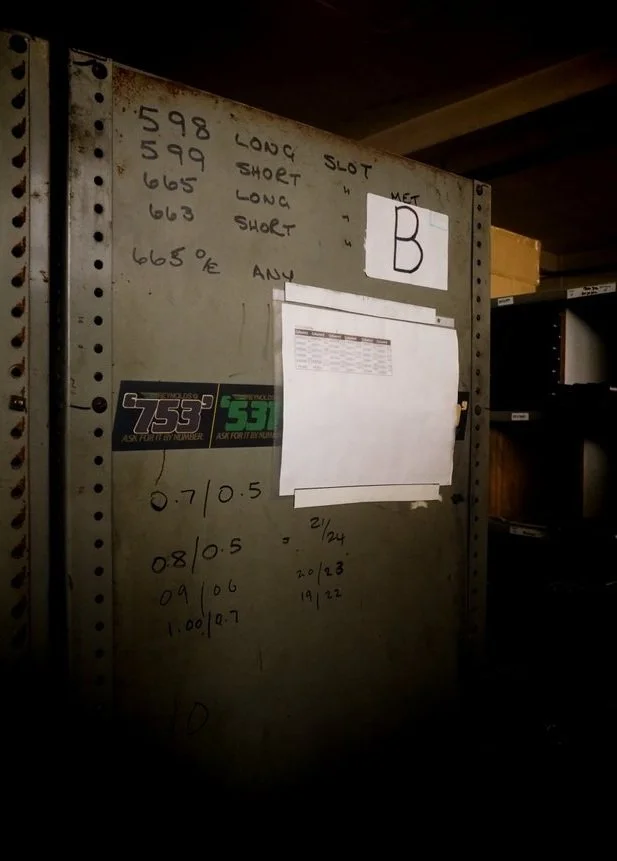

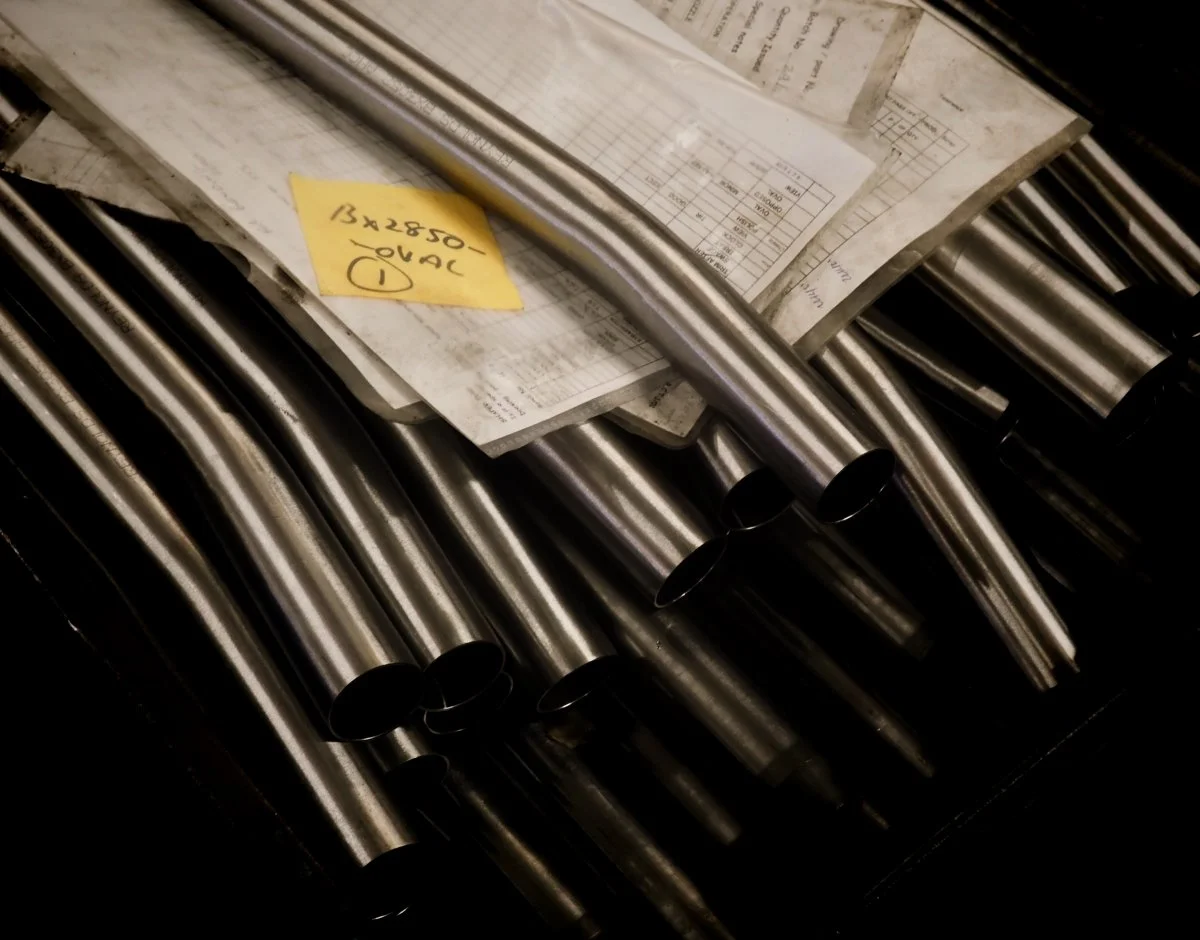
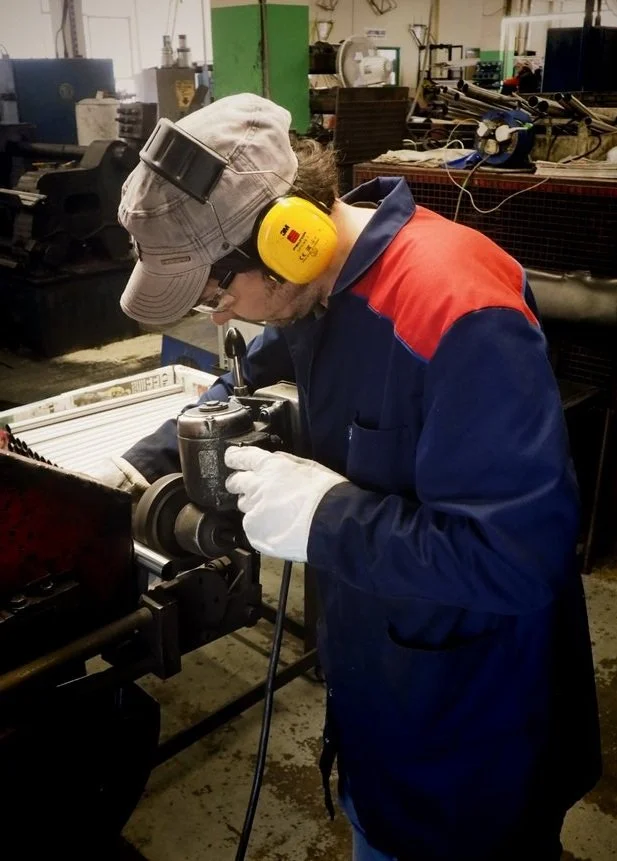

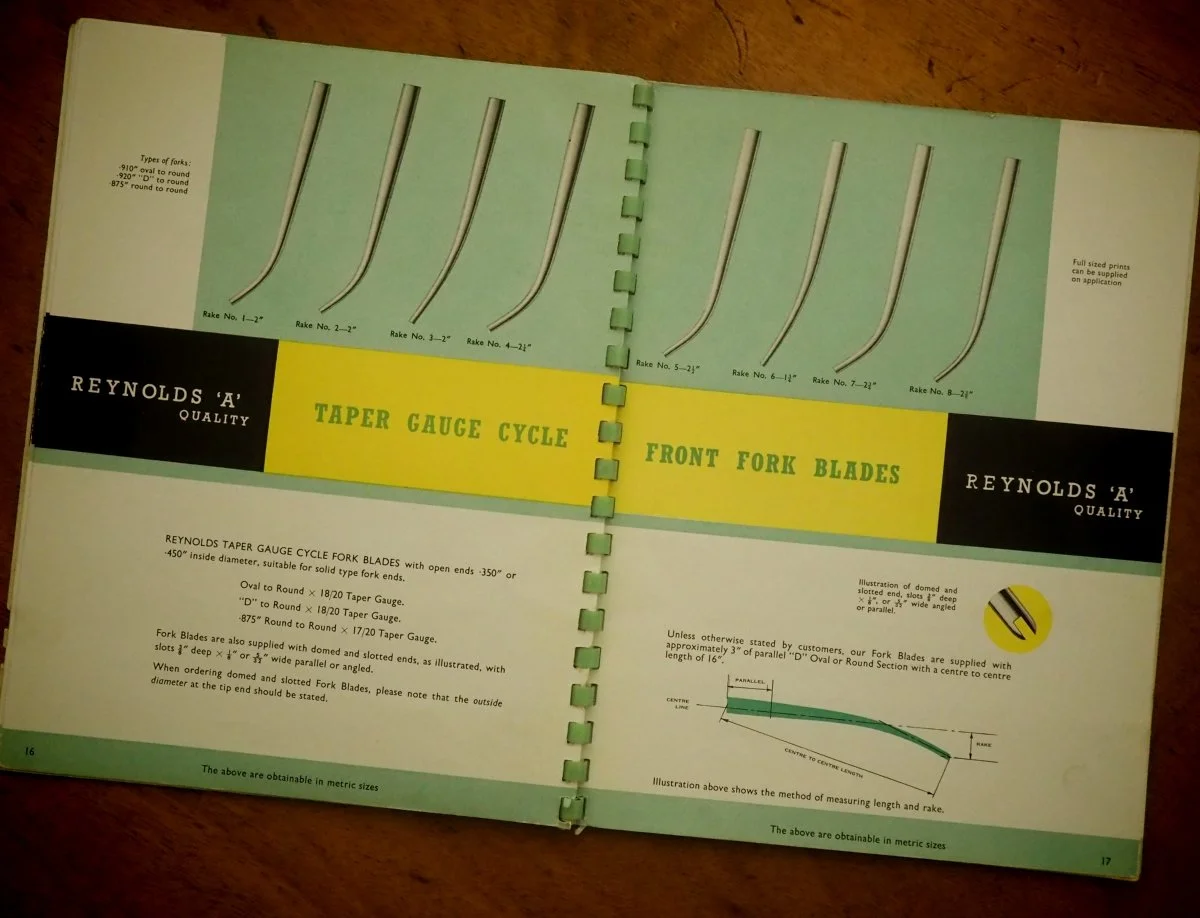
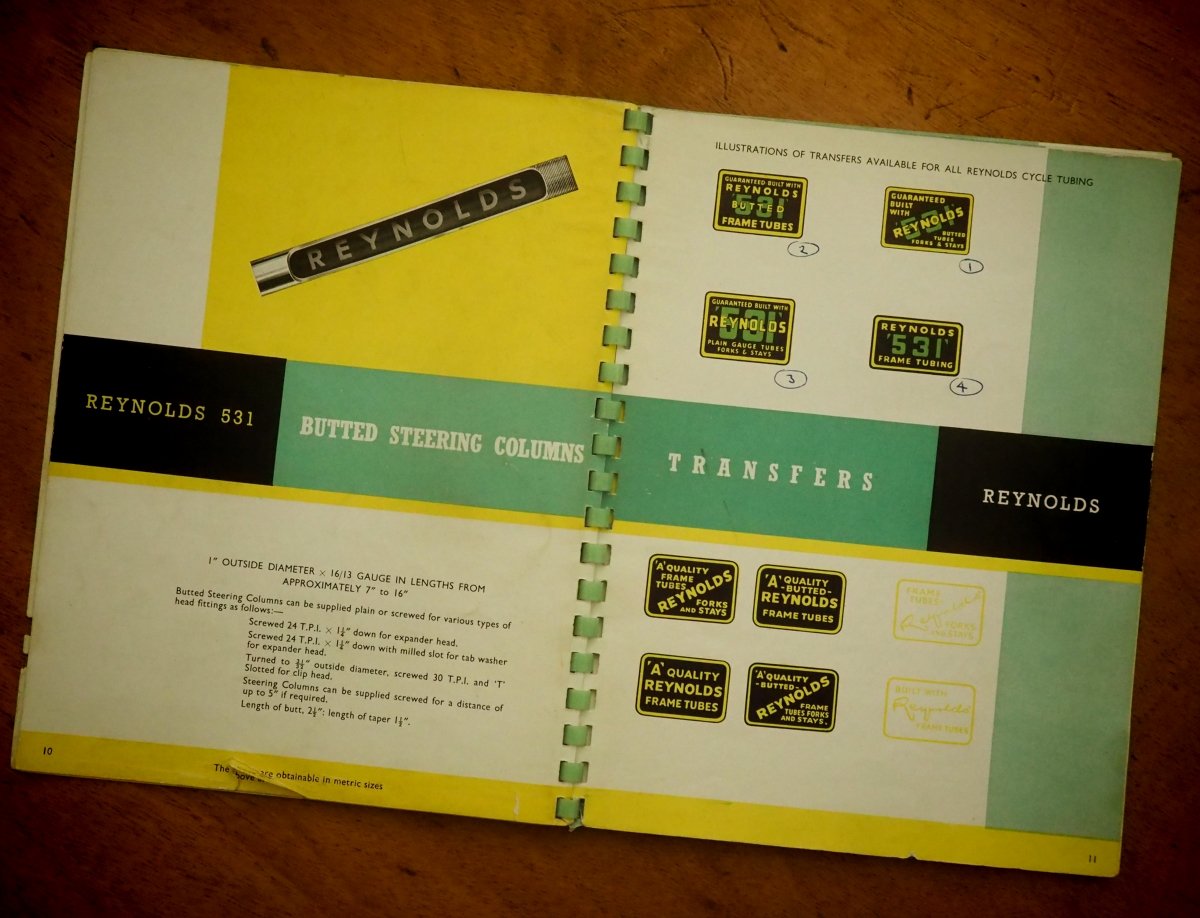